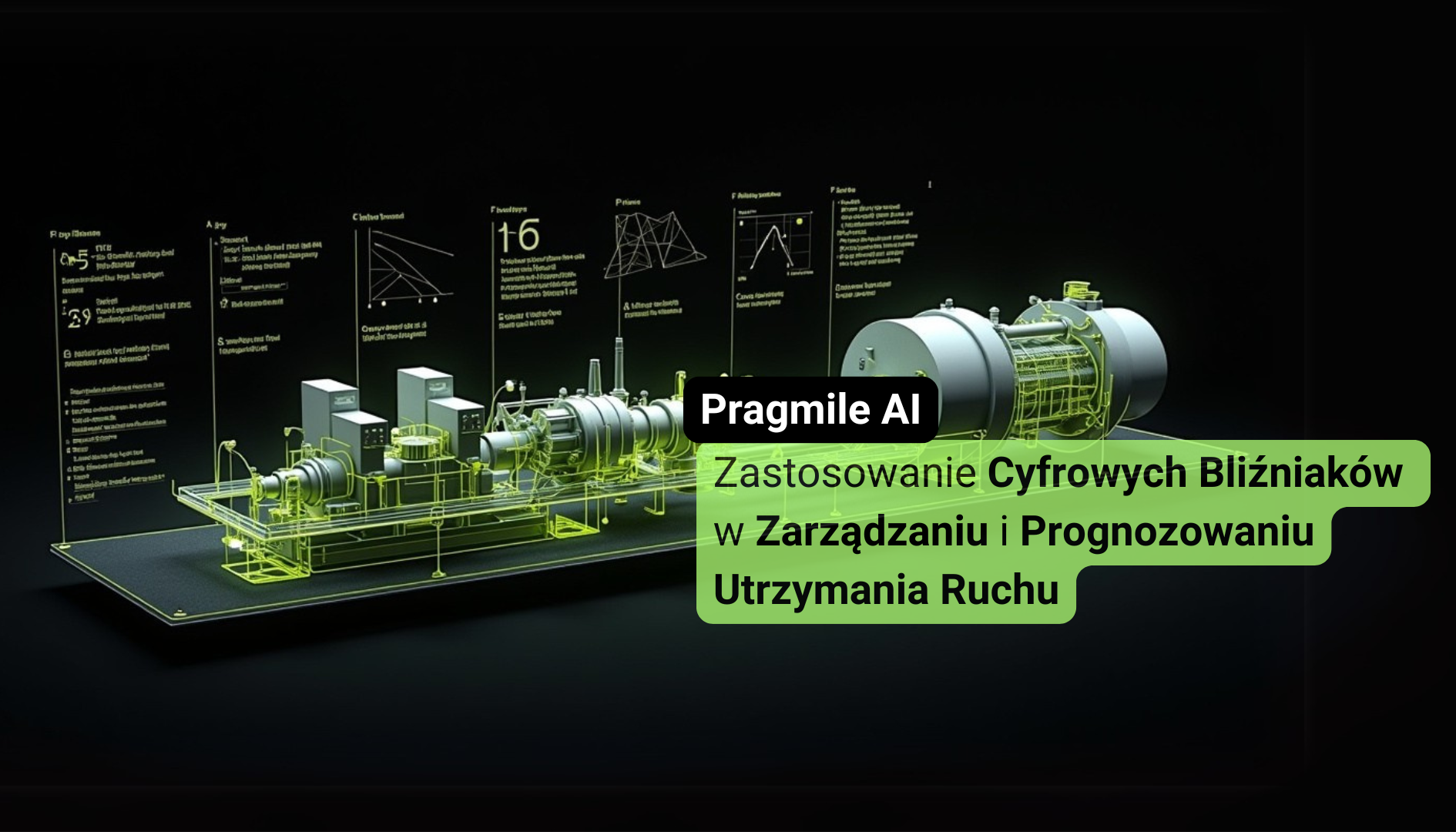
Data publikacji: 1 kwietnia 2025
Zastosowanie cyfrowych bliźniaków w zarządzaniu i prognozowaniu utrzymania ruchu
Współczesny świat jest coraz bardziej związany z technologiami cyfrowymi, które rewolucjonizują sposób, w jaki zarządza się i optymalizuje się procesy w różnych branżach. Jednym z najbardziej interesujących i dynamicznie rozwijających się obszarów jest zastosowanie cyfrowych bliźniaków w zarządzaniu i prognozowaniu utrzymania ruchu. Cyfrowe bliźniaki to zaawansowane modele wirtualne, które odwzorowują fizyczne obiekty, procesy lub systemy w czasie rzeczywistym. Ich rola w zarządzaniu utrzymaniem ruchu staje się coraz bardziej istotna, ponieważ pozwalają na precyzyjne monitorowanie stanu maszyn i przewidywanie awarii, co znacząco wpływa na efektywność operacyjną i redukcję kosztów. W dobie Przemysłu 4.0 integracja oprogramowania cyfrowych bliźniaków z systemami zarządzania produkcją i utrzymaniem ruchu staje się kluczowa dla przedsiębiorstw dążących do optymalizacji działań.
Czym jest utrzymanie ruchu?
Utrzymanie ruchu to zbiór działań mających na celu zapewnienie niezawodności i sprawności technicznej maszyn, urządzeń i systemów produkcyjnych. Jest to kluczowy element strategii zarządzania produkcją, który obejmuje konserwację, diagnostykę oraz naprawy sprzętu. W zależności od podejścia utrzymanie ruchu może przybierać różne formy:
- Utrzymanie reaktywne (konserwacja reaktywna) – naprawa sprzętu dopiero po wystąpieniu awarii.
- Utrzymanie prewencyjne (konserwacja prewencyjna) – okresowe przeglądy i konserwacja mające na celu zapobieganie awariom.
- Utrzymanie predykcyjne (konserwacja predykcyjna, utrzymanie proaktywne) – wykorzystanie nowoczesnych technologii, takich jak cyfrowy bliźniak napędzany AI, do przewidywania usterek na podstawie analizy danych.
Współczesne podejście do utrzymania ruchu opiera się coraz częściej na predykcji, gdzie technologie takie jak cyfrowy bliźniak i IoT pozwalają na bieżące monitorowanie pracy maszyn i optymalizację działań serwisowych.
Cyfrowy bliźniak – co to jest i jak działa?
Cyfrowy bliźniak to wirtualna replika fizycznego obiektu, systemu lub procesu. Może to być maszyna, cały zakład produkcyjny, sieć transportowa lub nawet cały łańcuch dostaw. Dzięki integracji danych z czujników IoT, modelowaniu 3D i analizie danych, cyfrowy bliźniak wiernie odzwierciedla stan i zachowanie swojego fizycznego odpowiednika. To wirtualne odwzorowanie umożliwia symulowanie zachowań, testowanie różnych scenariuszy i optymalizowanie działań bez ryzyka uszkodzenia lub zakłócenia pracy fizycznych systemów.
Do podstawowych funkcji cyfrowych bliźniaków należą przede wszystkim:
- Monitorowanie stanu technicznego w czasie rzeczywistym – bieżące śledzenie parametrów pracy maszyn, takich jak temperatura, wibracje czy zużycie energii, gromadzenie tych informacji i analiza danych operacyjnych.
- Diagnostyka i prognozowanie awarii – analiza danych historycznych i bieżących w celu przewidywania potencjalnych usterek.
- Symulacja – modelowanie zachowań urządzeń i procesów.
- Optymalizacja procesów – analiza wydajności maszyn oraz identyfikacja wąskich gardeł.
- Integracja z systemami zarządzania produkcją – możliwość analizy w kontekście całej linii produkcyjnej.
- Optymalizacja planowania przeglądów i napraw – planowanie działań konserwacyjnych w oparciu o rzeczywisty stan techniczny maszyn, a nie sztywne harmonogramy.
- Redukcja kosztów utrzymania ruchu – minimalizacja przestojów i kosztów napraw poprzez predykcyjne utrzymanie ruchu.
Wartość globalnego rynku cyfrowych bliźniaków (LINK) została oszacowana na 17,73 mld USD w 2024 roku. Przewiduje się, że wzrośnie z 24,48 mld USD w 2025 r. do 259,32 mld USD do 2032 r.
Digitalizacja procesów oraz digitalizacja produkcji i ich rola w utrzymaniu ruchu
Digitalizacja procesów i digitalizacja produkcji są kluczowymi elementami wdrażania cyfrowych bliźniaków. W ramach Przemysłu 4.0, który promuje wykorzystanie zaawansowanych technologii do zwiększenia wydajności i efektywności, cyfrowe bliźniaki odgrywają centralną rolę. Pozwalają one na digitalizację produkcji, umożliwiając wirtualne testowanie nowych produktów i procesów przed ich fizycznym wdrożeniem, co znacznie redukuje koszty i czas rozwoju.
Wdrożenie digitalizacji produkcji i digitalizacji procesów w kontekście utrzymania ruchu pozwala firmom na bardziej efektywne zarządzanie infrastrukturą techniczną. Tradycyjne metody utrzymania ruchu bazują na interwencjach reaktywnych (naprawa po awarii) lub prewencyjnych (okresowe przeglądy), co może prowadzić do niepotrzebnych kosztów i przestojów.
Dzięki zastosowaniu cyfrowych bliźniaków możliwe jest przejście na model konserwacji predykcyjnej – przewidywania i zapobiegania awariom jeszcze przed ich wystąpieniem. Kluczowe korzyści takiego podejścia to:
- Zmniejszenie liczby awarii poprzez ich wcześniejsze wykrywanie
- Lepsza alokacja zasobów serwisowych
- Zmniejszenie nieplanowanych przestojów produkcyjnych
- Wydłużenie żywotności sprzętu
Korzyści z wdrożenia cyfrowych bliźniaków w utrzymaniu ruchu
Implementacja cyfrowych bliźniaków w systemach utrzymania ruchu niesie za sobą szereg korzyści, zarówno w zakresie efektywności operacyjnej, jak i kosztowej. Do najważniejszych z nich należą następujące:
- Redukcja przestojów – precyzyjne przewidywanie awarii pozwala na ich eliminację, zanim wpłyną na proces produkcji.
- Zmniejszenie kosztów operacyjnych – optymalizacja harmonogramów konserwacji i lepsza kontrola nad zużyciem komponentów. Możliwość testowania wirtualnych scenariuszy redukuje koszty związane z fizycznymi testami i awariami.
- Zwiększenie efektywności energetycznej – monitorowanie parametrów operacyjnych urządzeń pozwala na redukcję zużycia energii.
- Integracja z systemami IoT – wykorzystanie cyfrowych bliźniaków w połączeniu z IoT umożliwia gromadzenie i analizowanie danych w czasie rzeczywistym.
- Poprawa jakości produktów – precyzyjna kontrola nad procesami produkcyjnymi prowadzi do minimalizacji defektów.
- Zwiększenie bezpieczeństwa – monitorowanie stanu technicznego maszyn i urządzeń w celu zapobiegania wypadkom.
- Zwiększona wydajność – cyfrowe bliźniaki pozwalają na optymalizację procesów, co prowadzi do zwiększenia wydajności i produktywności.
- Zapobieganie awariom – prognozowanie awarii pozwala na zaplanowanie konserwacji w sposób, który nie zakłóci pracy.
NVIDIA Omniverse™ Blueprint – cyfrowe bliźniaki w przemyśle
Jednym z przełomowych rozwiązań w zakresie cyfrowych bliźniaków jest NVIDIA Omniverse™ Blueprint, (LINK), które umożliwia tworzenie interaktywnych modeli symulacyjnych w czasie rzeczywistym. Platforma ta została zaprojektowana w celu wspierania przemysłowych wdrożeń cyfrowych bliźniaków poprzez integrację zaawansowanej fizyki, sztucznej inteligencji oraz technologii wizualizacji 3D. Rozwiązanie wykorzystujące inżynierię wspomaganą komputerowo (Computer Aided Engineering, CAE) jest dedykowane deweloperom oprogramowania przemysłowego, by mogli pomagać swoim klientom z branży lotniczej, motoryzacyjnej, produkcyjnej, energetycznej i innych gałęzi przemysłu obniżać koszty rozwoju i zużycie energii, a przy tym szybciej wprowadzać produkty na rynek.
Jednym z pierwszych zastosowań tego projektu są symulacje obliczeniowej dynamiki płynów (Computational Fluid Dynamics, CFD). Stanowi to kluczowy krok do wirtualnego eksplorowania, testowania i udoskonalania projektów samochodów, samolotów, statków oraz wielu innych produktów.
Tradycyjne procesy prac inżynierskich – począwszy od symulacji fizyki, skończywszy na wizualizacji i optymalizacji projektu – potrafią trwać tygodniami, a nawet miesiącami. NVIDIA i Luminary Cloud jako pierwsi w branży zademonstrowali wirtualny tunel aerodynamiczny, który umożliwia użytkownikom symulację i wizualizację dynamiki płynów w czasie rzeczywistym, przy interaktywnych prędkościach, nawet podczas zmiany modelu pojazdu wewnątrz tunelu.
Dzięki wykorzystaniu technologii NVIDIA Omniverse™ Blueprint, przedsiębiorstwa mogą testować i optymalizować procesy produkcyjne w pełni wirtualnym środowisku, minimalizując ryzyko błędów i zwiększając elastyczność operacyjną. Tego typu rozwiązanie z powodzeniem mogłoby znaleźć swoje zastosowanie również w realistycznym modelowaniu procesów produkcyjnych, analizie wpływu warunków operacyjnych na maszyny czy przewidywaniu awarii. Jest to jeden z kluczowych kroków w kierunku pełnej integracji cyfrowych bliźniaków z Przemysłem 4.0, zapewniający przewagę konkurencyjną firmom, które stawiają na digitalizację produkcji.
Jeśli interesuje Cię zgłębianie tematu zastosowania cyfrowych bliźniaków w zarządzaniu i prognozowaniu utrzymania ruchu oraz w innych obszarach biznesowych, już teraz zarezerwuj bezpłatną konsultację z Marcinem Jabłonowskim – Dyrektorem Zarządzającym i Architektem Rozwiązań AI w Pragmile.
Umów się na bezpłatną konsultację z
naszymi ekspertami AI i technologii
Skorzystaj z najnowszych rozwiązań AI, dopasowanych do potrzeb Twojej firmy. Zarezerwuj konsultację z architektami rozwiązań AI w Pragmile i odkryj nowe możliwości w zarządzaniu energią.
Aby umówić się na spotkanie, podaj swój e-mail firmowy