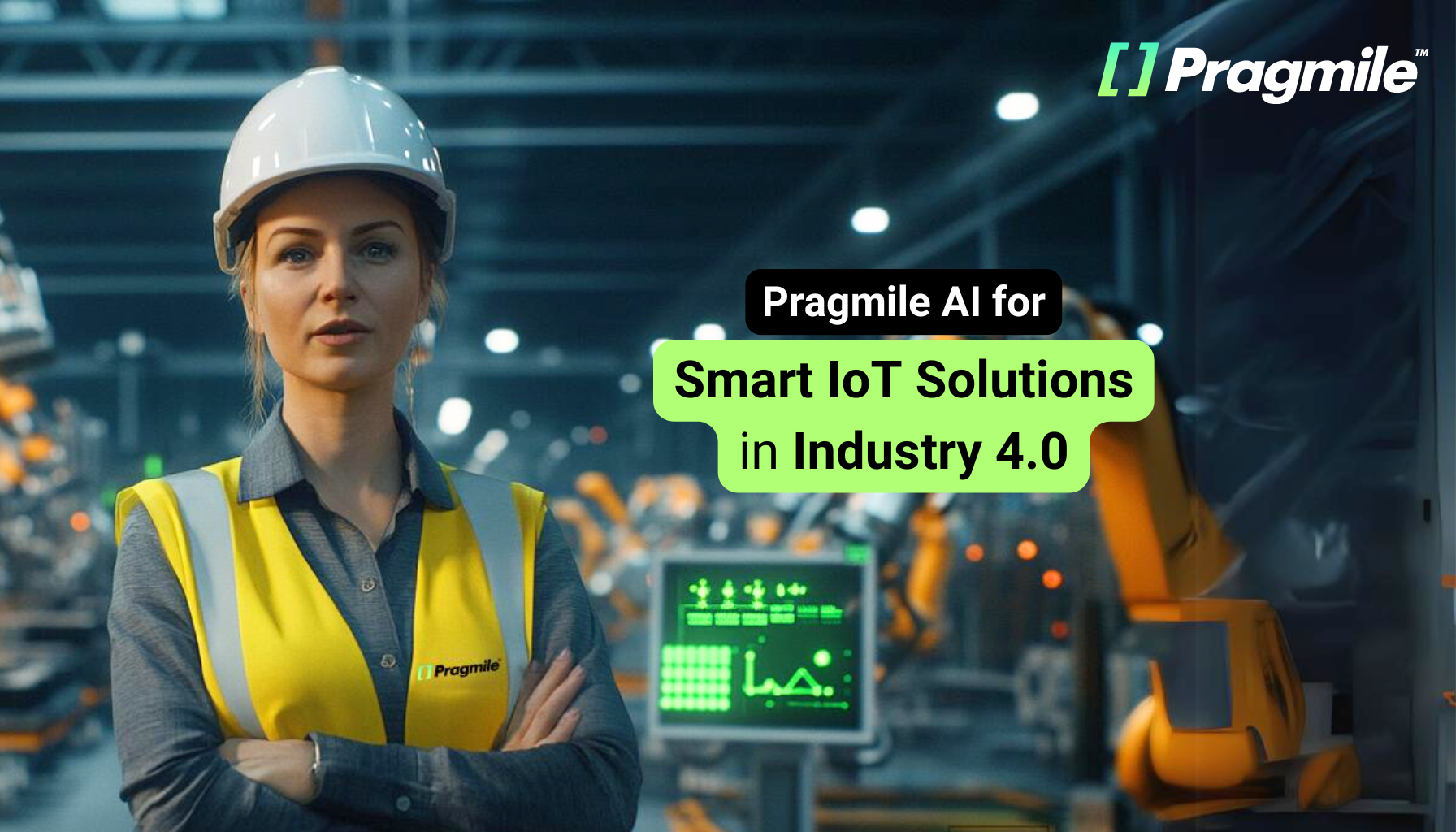
Date published: August 20, 2024
Harnessing IoT and AI to Minimize Production Interruptions
Industry 4.0 Technologies: Harnessing IoT in Manufacturing with AI to Reduce Production Downtime
In the high-stakes world of industrial manufacturing, every second counts. When production grinds to a halt—whether due to equipment failure, human error, or supply chain hiccups—the costs can quickly spiral. Not only do these interruptions eat into profits, but they also ripple through supply chains, creating delays that leave customers frustrated and competitors circling. It’s no wonder, then, that the industry is turning to cutting-edge technologies like the Internet of Things (IoT) and artificial intelligence (AI) to keep the wheels of production turning smoothly.
The Persistent Problem of Production Interruptions
Production downtime has long been the Achilles’ heel of the manufacturing sector, leading to inefficiencies, inflated costs, and diminished competitiveness. Unplanned interruptions in production—whether caused by machine failures, raw material quality issues, human error, or logistical challenges—can result in substantial financial losses, delayed deliveries, and unsatisfied customers. Moreover, downtime in one facility often sets off a domino effect, disrupting the entire supply chain.
The complexity of today’s production processes only amplifies the challenge of pinpointing and preventing these interruptions. In a hyper-competitive global market, where the pressure to optimize efficiency and cut costs is relentless, minimizing downtime is no longer just an operational goal; it’s a business imperative.
That’s why forward-thinking companies are increasingly investing in IoT and AI technologies. These tools not only monitor and analyze production processes but also provide actionable insights that help manufacturers preempt and address potential issues before they escalate. According to McKinsey, leveraging these technologies can reduce machine downtime by 30-50%, boost labor productivity by 15-30%, increase throughput by 10-30%, and even improve forecasting accuracy by up to 85%.
Industry 4.0 IoT: The Eyes and Ears of Modern Production
At the heart of the Industry 4.0 revolution is the Internet of Things—a vast network of connected devices that communicate with each other and with centralized systems to share real-time data. In an industrial setting, IoT encompasses a wide array of sensors and devices installed on machines throughout the plant. These sensors monitor everything from temperature and humidity to speed, vibrations, pressure, and energy consumption, providing a continuous stream of operational data.
But IoT isn’t just about machines. It also extends to tracking employee behavior and interactions with equipment. For instance, wearable devices can monitor workers’ physical activity, helping to identify ergonomic issues or lapses in productivity. IoT can also track how quickly employees respond to alarms or whether they adhere to maintenance protocols. This comprehensive data collection lays the groundwork for AI-powered analysis that can revolutionize how production processes are managed.
AI: Transforming Data into Actionable Insights
While IoT gathers the data, artificial intelligence is the engine that transforms this raw information into meaningful insights. Using advanced machine learning algorithms, AI can analyze massive datasets, uncovering patterns, trends, and anomalies that might indicate potential production issues. By doing so, AI enables predictive maintenance, allowing manufacturers to address problems before they lead to costly downtime.
AI’s capabilities extend beyond just machinery. By analyzing employee behavior data, AI can identify workflow inefficiencies, pinpoint areas where additional training is needed, or even suggest changes to improve overall productivity. For example, AI can detect subtle changes in machine operation—like an increase in vibration—that may signal an impending failure, enabling preemptive action. AI can also analyze historical data to predict when specific machine models are likely to fail, allowing for more strategic maintenance scheduling.
Tackling Downtime with IoT and AI: Real-World Strategies
By combining IoT and AI, manufacturers can effectively identify the root causes of downtime and implement strategies to minimize it. Some common scenarios include:
- Equipment Failures: By monitoring machine conditions in real time, IoT sensors can detect early signs of wear and tear or improper operating conditions. AI then analyzes this data to predict when a failure is likely to occur, allowing for timely maintenance and reducing the risk of unexpected breakdowns.
- Process Inefficiencies: AI can analyze production data to identify bottlenecks or inefficient workflows, suggesting optimizations that can streamline operations and boost productivity.
- Human Errors: By monitoring employee interactions with machinery, IoT devices can flag improper usage or deviations from standard procedures. AI can then recommend targeted training or suggest process adjustments to reduce errors and improve safety.
- Quality Issues: IoT sensors can detect real-time fluctuations in material quality or environmental conditions, while AI analyzes this data to prevent defects from occurring, ensuring consistent product quality.
- Supply Chain Disruptions: By continuously monitoring material flows, IoT and AI can identify potential supply chain issues before they impact production, allowing for proactive problem-solving.
The Tangible Benefits of IoT and AI in Production
The integration of IoT and AI into production processes offers several compelling benefits:
- Increased Efficiency: Real-time monitoring and process optimization lead to better resource utilization, reduced downtime, and faster production cycles.
- Cost Reduction: Preventative maintenance and optimized resource management help cut costs associated with emergency repairs and production losses.
- Enhanced Quality Control: Automated monitoring and early defect detection ensure consistently high-quality outputs.
- Informed Decision-Making: Access to accurate, up-to-date data empowers managers to make better, faster decisions and respond proactively to emerging challenges.
Siemens Electronics Works Amberg: A Case Study in Smart Manufacturing
One of the leading examples of IoT and AI in action is Siemens Electronics Works Amberg (EWA), a cutting-edge digital factory that exemplifies Industry 4.0. At EWA, Siemens leverages its cloud-based IoT system, Insights Hub (formerly MindSphere), to collect and analyze data from a vast array of sensors embedded in production machinery.
This data, processed by AI algorithms, enables predictive maintenance by identifying early signs of potential failures, thus preventing costly downtime. For instance, EWA replaced traditional X-ray inspections of printed circuit boards with an AI model that analyzes sensor data to predict defects, allowing production to continue uninterrupted.
Moreover, AI and Industrial Edge technology are employed to monitor milling spindle performance, analyzing speed and power consumption to detect anomalies that could lead to machine failures. This system can alert operators 12-36 hours in advance, giving them ample time to take preventive measures.
The results speak for themselves: Siemens’ implementation of IoT and AI at EWA has led to significant improvements in production efficiency and quality, demonstrating how these technologies can enhance competitiveness and adaptability in today’s industrial landscape.
Pragmile: Solar Spy Digital Twin Technology with IoT
Another great example of innovation in this field is Pragmile’s development of a comprehensive digital twin for Solar Spy—an advanced, AI-driven system that autonomously monitors and diagnoses the performance of large solar farm portfolios by leveraging IoT and cloud-based data. The platform furthermore integrates thermal drone imaging with AI analysis to optimize energy production and proactively identify potential issues in photovoltaic farms.
This cutting-edge platform also harnesses AI to forecast energy production and mitigate losses during periods of negative energy pricing, all through remote site control capabilities. Building on Pragmile’s expertise in prescriptive analytics, the ongoing enhancements to this platform promise to deliver unprecedented efficiency levels in the renewable energy industry.
Looking Ahead: The Future of IoT and AI in Industry
The journey of integrating IoT and AI into manufacturing is just beginning. As these technologies evolve, we can expect even greater advancements, such as the widespread adoption of digital twins, augmented reality, and edge computing. These innovations will further expand the capabilities of IoT and AI, offering new ways to optimize production and minimize downtime.
As we look to the future, it’s clear that the industrial sector is on the brink of a transformation where downtime becomes increasingly rare, and production becomes more efficient, flexible, and sustainable. The fourth industrial revolution is here, and companies that embrace Industry 4.0 will be well-positioned to lead the market.
For businesses looking to harness the power of IoT and AI, partnering with experts like Marcin Jabłonowski, Pragmile’s Managing Director and AI Solutions Architect, can be the key to staying ahead in this rapidly evolving landscape. With the right guidance, your organization can successfully navigate the complexities of digitization and automation, ensuring a competitive edge in the future of industry.
Schedule a free consultation with
our AI and technology experts
Take advantage of the latest AI solutions, tailored to your company's needs. Book a consultation with AI solution architects at Pragmile and discover new opportunities in energy management.
Please, provide your business email to schedule a meeting